The Art and Science of Navigating China Inspection Services
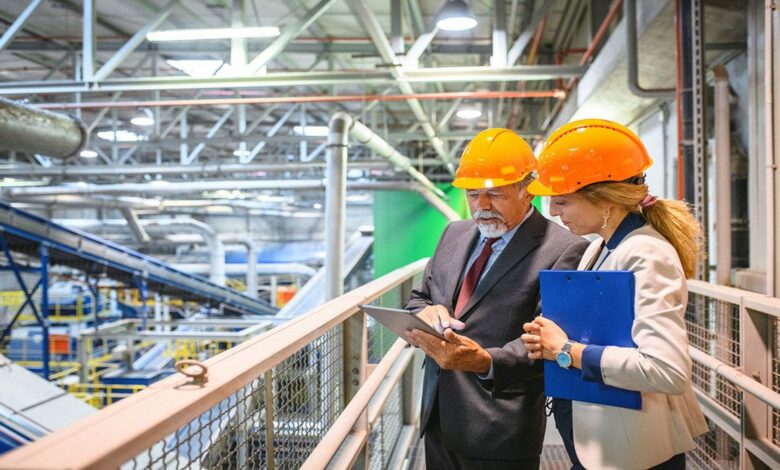
When it comes to manufacturing, China is undoubtedly a global titan. However, the process of quality control through inspection services can be labyrinthine for the uninitiated. This blog post will explore the unique complexities of navigating China inspection services and present practical solutions for overcoming these challenges.
What Are China Inspection Services?
China inspection services are vital to worldwide trade. They are the watchdogs of product quality, making sure items shipped globally comply with standards. By pinpointing areas for improvement, they help businesses make their products better.
But it’s no easy job. Inspecting different products—electronics, toys, textiles, machinery—takes various approaches. Each product line has its own rules. It’s like conducting an orchestra where every performance should be flawless to please the international audience.
These services also offer necessary neutrality. This fair treatment ensures products, big or small, from any business, are evaluated using the same quality measures. Acting as guardians of worldwide trade, they make sure items with the ‘Made in China’ tag meet global standards. Grasping this service can unlock its full potential.
Understanding China’s Inspection Services
Working with China’s inspection services can be tough. The main problem? Language. Language issues can cause misunderstandings between the inspection team and client. This confusion can cause mistakes during inspections. China’s business traditions can make things more difficult as well.
Another issue is China’s size. Its huge size means inspection rules and standards change from place to place. This can lead to uneven inspection outcomes.
China’s fast-moving manufacturing sector needs quick inspections. But managing inspections in this fast-paced world can be hard. It’s a real test for inspection services’ efficiency.
Lastly, the many types of products made in China need different types of inspections. Whether it’s electronics, textiles, toys, or machinery, each needs a certain inspection process. This calls for expertise and an eye for detail. Dealing with China’s inspection services can be tough and needs problem-solving skills.
Breaking Down Language Walls
When dealing with inspections in China, language differences can pose some challenges. Overcoming this involves using both tech tools and human help. Hiring staff who speak both languages or using translation services can help. It’s also a good idea to teach your team some language skills.
Thanks to modern tech, we have loads of tools available. Translation apps, which often have voice recognition, can translate instantly. This keeps dialogue flowing. Online language courses can also help staff keep improving. This means they can talk more confidently in an international business context.
When tackling language problems, it’s important to understand the words used in this sector. This means not just translating words, but also understanding what technical terms mean in the inspection industry. One way to do this is to make a glossary of terms. Keeping it up-to-date is important, given the fast-paced nature of the manufacturing world.
Breaking through language obstacles when dealing with China inspection services means combining human and digital efforts. This, backed by knowledge of industry-specific words, improves communication and makes inspection more accurate and effective.
Creating Uniform Inspection Standards for Different Regions
Dealing with different inspection standards in various markets can be confusing. To solve this, it’s essential to create standard inspection criteria. It’s about setting measurable quality and safety standards that don’t change no matter the market.
Take a toy-making company, for instance. By setting defined standards like using safe materials and sturdy design, quality doesn’t change, regardless of where the toy ends up. Inspectors can check all products against these fixed quality points.
Standardizing also means that all products meet the same high-quality tests, no matter where they go. This reduces the chance of different quality levels in different markets and strengthens a company’s reputation for consistency.
Uniform inspection rules also make the inspection process simple. Inspectors don’t need to change their assessment guidelines for different markets, making inspections more straightforward and efficient.
It takes time and effort to standardize things. But it’s totally worth it! It shows we’re serious about making great stuff. Plus, our customers all around the world trust us more. It’s a big part of how we succeed.
Making Inspections Work in Different Places
China is huge, so inspecting things in different parts can be tough. Each province has its own way of doing things which can be tricky. That’s why we need to have a hub where everything is managed. Picture a digital command center giving live updates about inspections. This way, we’d be able to see and react to problems fast. Plus, a shared communication system could make teams work together better. With this setup, we’d know who’s available to inspect and where they are. Think of it like a conductor and an orchestra. Each part works together to make beautiful music. In our case, successful inspections. The awesome technology of today can help make this happen. This turns a big challenge into something easier. It’s an important step in mastering inspections in China’s provinces.
Utilizing Tech for Smoother Inspections
These days, tech is the tool that makes inspections more efficient. It’s like an orchestra, with every instrument, big or small, playing its part for a beautiful finish. In the same way, a digital platform can be the conductor. It helps in smooth communication and data sharing between factories and inspection services. This makes the work faster and reduces the chance of misunderstanding or data loss.
And tech doesn’t stop there. New equipment such as drones and robots have changed the game for inspecting hard-to-reach places. Areas once deemed unreachable are now accessible to the inspector thanks to the devices. Think of a drone flying high, capturing full aerial shots, or a small robot slipping into a tight space, shining a light on unseen issues.
Then there are AI-based analysis tools, another innovation in quality control services. These tools can handle tons of data quickly, finding patterns and odd things that could slip past a human inspector. This boosts the accuracy of inspections and introduces predictive analytics. It helps catch potential problems before they turn into real issues.
Technology has remodeled the inspection field, converting tough tasks into manageable problems and leading the shift towards effective inspection services.
Final Thoughts
Navigating the intricate scene of China’s inspection services requires both an art and a science. It requires an in-depth understanding of local customs, language, and business norms, along with a strategic approach to handle obstacles. Although it might seem tough, mastering this can yield significant rewards like top-notch product quality, stronger brand reputation, and increased consumer trust.
Using tools such as language skills improvement, standardizing inspection criteria, and technological advancement can change the complex maze of China’s inspection services into a clear pathway to success. This journey is worth taking. It sets up not just a product’s approval but also upholding China’s promise of excellent quality. It’s a way to guarantee that each product from Chinese production lines upholds first-rate quality and safety, setting a global standard.
In the changing setting of China’s inspection services, being adaptable, innovative, and understanding cultural and technical subtleties can take challenges and turn them into prospects. Through constant learning and innovation, we can master navigating China inspection services, contributing overall to the global promise of quality and safety.